Section 4
Choosing the right Drill Bits
When drilling with the LS-100, there are two basic sizes of drill bits: 10 cm (4 in) and 15 cm (6 in). Usually a 10 cm drill bit is used to drill a pilot hole (especially in hard formations). This
maximizes drilling speed and gives the drilling crew a "preview" of subsurface conditions. Given the limited power of the LS-100, wells are commonly extended into rock using a 10 cm hole which is left uncased (a 15 cm hole should be drilled several feet into the rock to firmly seat the surficial casing). In overburden and soft rock formations, 15 cm bits are used to ream the pilot hole open wider so that the casing (Section 7), filter pack (Section 8), and grout annual seal (Section 9) can be placed. A 15 cm bit can be used without first drilling a pilot hole where drilling is easy, the water table close to surface or subsurface conditions are well known. |
Three general types of bits are used when drilling with the LS-100: the drag (blade or fishtail) bit, the roller (or tricone) bit and reamer bits (see Figure 7).
Drag bits have short blades, each forged to a cutting edge and faced with tungsten carbide tips. Short nozzles direct jets of drilling fluid down the faces of the blades to clean and cool them (Driscoll, 1986). A blade bit is a drag bit in which the blades can be replaced. Drag bits have a shearing action and cut rapidly in sands, clays and some soft rock formations. Most drilling is done using the Drag bit (especially in clay and sands). However, it does not work well in coarse gravel or hard-rock formations. Whenever
possible, drag bits should be used to drill pilot holes because they produce cuttings which are easiest to log. |
Roller bits have three or more cones ("rollers" or "cutters") made with hardened steel teeth or tungsten carbide inserts of varied shape, length and spacing. They are designed so that each tooth applies pressure at a different point on the bottom of the hole as the cones rotate. The teeth of adjacent cones intermesh so that self-cleaning occurs. The cutting surfaces of all roller bits are flushed by jets of drilling fluid directed from the inside (centre) of the bit. Roller bits exert a crushing and chipping action, making it possible to cut hard rock formations (Driscoll, 1986). If possible, use roller bits for reaming the 10 cm pilot hole open to 15 cm because they produce minimal amounts of clay smearing etc on borehole walls. |
The three roller Tricone bit is the most common roller bit. It has conically shaped rollers on spindles and bearings set at an angle to the axis of the bit. It is used as an all-purpose bit in every type of formation.
As a general rule, hard rock roller bits should be used at much slower speeds and higher bit weight than blade bits used for drilling soft formations.
A REAMER BIT is later used to widen the hole to 15.24 cm (6 in). A reamer bit consists of hardened cutting surfaces attached to drill pipe; it is screwed just above the drill bit. A reamer bit is used in sandy soils or in clay if the roller bit becomes too gummed-up with clay and/or there are problems keeping the hole straight. A 10.16 cm (4 in) roller or blade bit is fitted ahead of the reamer bit and runs in the existing 10.16 cm pilot hole. This makes it easy to keep the borehole very straight during the reaming process.
Figure 7: Types of Drill Bits
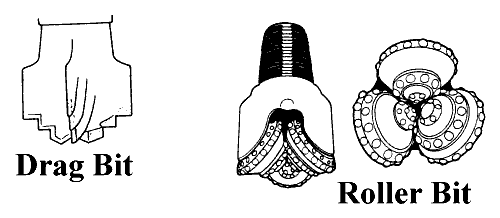
References
Driscoll, F. (1986) Groundwater and Wells, St. Paul: Johnson Division

Choose Another Well Construction Module:
|