Appendix M
Iron & Turdidity Treatment
Iron and Manganese Treatment
Iron and manganese is naturally present in many aquifers throughout the world. While iron can start causing aesthetically undesirable taste and odour problems at concentrations above 0.3 ppm, concentrations of up to 3.0 ppm are often acceptable to local people; higher levels could cause people to revert to traditional unprotected sources (Patnaik, 1987).
If people are not willing to drink the water because of the bitter, metallic taste or reddish staining caused by high iron levels, then treatment of the water should be attempted using one of the following procedures. It should be remembered, however, that the well screen may rapidly become encrusted with iron deposits, reducing the yield and finally causing failure of the well (Patnaik, 1987). In addition, iron deposits in the cylinders of deep well handpumps accelerate the wear on leather cup seals.
In many cases aeration causes dissolved iron to form fine particles which can be removed by filtration through sand. As described by Patnaik (1987), the Danish International Development Agency has developed a low maintenance filter which has been proven effective in treating iron concentrations as high as 32 ppm (see Figure 30)!
The unit consists of a 1.5 m high cylinder which is installed directly below the down-spout of the pump cylinder which is mounted on a raised platform or mound. Water is pumped onto a perforated aerator tray and then flows upwards thorough a layered series filter and sand layers. The filter media is cleaned by opening a valve or removing a flange so that water flows quickly down through the sand, flushing out the accumulated deposits.
Figure 30: Iron Removing Filter
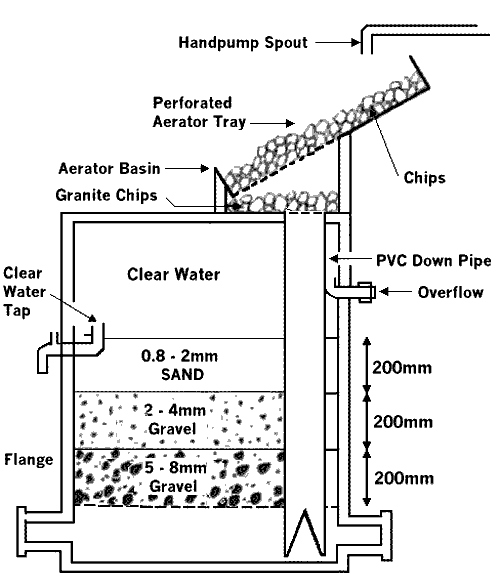
Turbidity Treatment
Wells screened in clay, silt, or very fine sand may produce coloured or turbid water. These fine materials may partially plug the screen and reduce well yield and will cause excessive wear of the pump cylinder and rubbers. These problems can be addressed in several ways:
- Proper well development improves the sand-free quality of the well water and the water transmitting characteristics of the formation. In established wells, the appearance of sand may indicate that the wells have been overpumped and/or that much of the well screen has become plugged. Extensive re-development of the well can sometimes overcome these problems.
- Sand commonly enters wells if the openings of the well screen (slot size) are too large, if the gravel pack contains material which is too coarse or fine, if insufficient gravel pack material was placed around the screen or if the well screen was partially positioned against a formation layer of fine sand, silt or clay. If extensive re-development is not successful, positioning the pump cylinder 1 or 2 meters above the top of the well screen will sometimes reduce turbulence and prevent fines from being pulled into the well.
- If the water still does not clear, it can be simply treated by placing it in clean, covered containers and letting it sit for 12 to 24 hours. Water should then be dipped from the top, taking care not to agitate the contents. If possible, disinfect (chlorine) the water prior to use if possible. Thoroughly clean the jar prior to refilling.
- Turbidity can also be treated with a Horizontal-flow Roughing Filter. Raw water falls over a weir into a inlet chamber in which coarse solids settle and flow is evenly passed through a perforated separation wall. Water then flows horizontally through a sequence of coarse (25 mm), medium, and fine (4 mm) filter chambers. The filter boxes could be 1 - 2 meters wide; their length (extending up to 10 meters long) depends on the raw water quality and the hydraulic filter load (design velocity should be 1 m/hour). In general, 20 L of filter plus 10 L of sand should be used for every 30 L/day required treated water. After a year or so, the filter packs will become loaded with retained
solids and the media should be cleaned or replaced.
- If available and transportable (they are heavy and fragile), pre-formed screens consisting of a slotted pipe surrounded by resin bonded sand can be attached to the bottom of the pump cylinder. Whenever the cylinder is pulled to change pump leathers, the pump screen should be cleaned. It may be possible to make a screen by wrapping filter cloth around a slotted pipe. Depending on the availability of local materials, it may even be possible to insert a secondary filter media (sand) between the cloth and the slotted pipe.
- Finally, if nothing else works, try installing a secondary sand pack and well screen (with a smaller slot size) in the well. Lower a 3.8 - 5.1 cm (1.5 - 2 in) diameter pipe to the bottom of the well; the pipe should extend several feet above the top of the well screen. The pipe should have very fine slots or be wrapped with a filter cloth and the space between the pipe and the well casing/screen be filled with a uniform fine to medium grained sand. If the pipe blocks over time, both it and the inner sand pack could be washed from the well and a new pack inserted.
Choose Another Well Construction Module:
|